- Improve Cutting Speed, Yield, & Efficiency
- Extend Blade Life
- Improve Material Surface Finish
- Reduce Chipping, Thermal Stress
- Reduce Material Micro Cracking & Edge Damage
- Preserve Material True Micro Structure
- No Foam
- Non Staining
- Compatible with all filtration systems
- Non Corrosive
- Safe to handle and dispose
- Friendly to operator and environment
- 1 (one) Quart Bottles
- 1 (one) Gallon Bottles
- 5 (five) Gallon Pails
- 55 Gallon Drums
No. SMART CUT Dicing Coolant was specifically designed and developed for semiconductor industry. While soaps leave residues and an cause contamination, SMART CUT Dicing Coolant rinses free, without concern of sodium’s and other ingredients that may contaminate delicate circuitry. Yes proper filtration will not affect SMART CUT Dicing Coolant performance. SMART CUT Dicing Coolant is homogeneous mixture that will not settle during storage. Shelf life is indefinite. However as will al materials we suggest rotation your inventory. A standard metering pump, commercially available can be retrofitted into the dicing saw water lines. Optimum dilution rates are best determined in house. Every application and customer preference is different. For best results we recommend 100:1 dilution ration. Some customers have used higher dilution ratios, with good success. SMART CUT Dicing Coolant is compatible with all semiconductor materials such as silicon, GaAs, Inp, or ceramic wafers. As well as majority of semiconductor packages used today such QFN and BGA, and many others. Excessive concentration of coolant is detrimental to material and waste of resources. Most internal water supplies of most organizations measure approximately seventy dynes of surface tension. When dicing and back grinding wafers and packages the dynes should be targeted for the forty five to fifty range. Coolants can only lower surface tension to a specific amount. Therefore adding more coolant concentration will only cause excessive foaming and residual build up on the wafer. Also some microelectronic packages and semiconductor wafers have copper present in the package or the photo mask operation. High concentration of coolant will react with the copper, and oxidation process can develop. General oxidation problems will arise on the bon pads. However, the proper amount of coolant as recommended by coolant manufacturer, will pose no oxidation problems. To avoid undesired die bonding problems, the sure to thoroughly rinse the water after the dicing procedure is complete. Again the use of a quality coolant will assist in wafer cleaning and removal of the slurry film build up. Additionally it is recommended to consult with the die bonding engineers to receive feedback on the consistency of their process. Sometimes the inability to standardize die bonding parameters and capillaries can be attributed to dirty wafers, specifically dirty bond pads.
APPLICATION EXAMPLE
Before
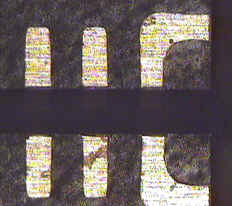
QFN Package Before use of SMART CUT Coolant
After

QFN Package After use of SMART CUT Coolant
Before
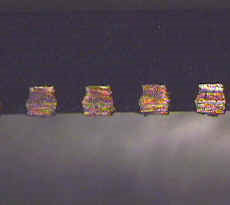
QFN Package Before use of SMART CUT Coolant
After
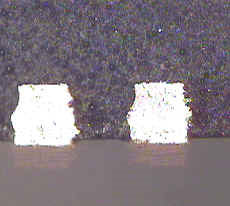
QFN Package After use of SMART CUT Coolant
SMART CUT® Dicing Coolant helps Semiconductor Package & Wafer Manufacturers
Reduces Surface Tension - by 25-40 dynes/cm2. SMART CUT KOOL allows more water into the material kerf / pores, dissipating heat generated by friction.
Bonds Water Molecules - into the kerf and to the diamond dicing blade, allowing better swarf dispersion and lubrication.
Prevent Swarf Accumulation - on the diamond dicing blade and in Back and frontside edges, minimizing chipping and internal cracking.
Extend Blade Life - by up to 30%. The lubricated dicing blade runs cooler, reducing fatigue and blade wear.
Improve Material Yield and Reliability - from the reduced amount of chipping, cracking and consequent edge damage.
Eliminate Additional Material Processing . Depending on the application and your objectives, SMART CUT Dicing Coolant frequently eliminates and minimizes secondary and subsequent material processing.
Improved Die Tolerances - Many of today's demanding package singulation and wafering dicing operations require very high precision tolerance. SMART CUT™ Dicing Coolant promotes attainment of close tolerances by removing heat generated at the point of contact between the dicing blade and substrate/wafer. Heat can cause deformations in both the blade and material that results in the loss of tolerance. When the generation of heat and its subsequent removal by a coolant is momentarily interrupted any coolant product will adversely affect the performance of a tool and therefore ruin a tolerance specification.
TOP 10 REASONS Why SMART CUT® Coolant is SUPERIOR
- Operator Sensitivity- SMART CUT KOOL is formulated with operator friendly additives that will not irritate skin (dermatitis), nasal passages, or eyes.
- Bio-resistance. SMART CUT KOOL is formulated with biocides and fungicides to biologically control the growth of bacteria, fungi, and mold in the coolant system. The bio-resistance will determine its suitability for recycling in large central systems.
- Corrosion Protection- SMART CUT KOOL is formulated with corrosion inhibitors, which provide protection to machinery and the substrate. The protection needed will be determined by the customers requirements. With proper concentration, no corrosion should occur on the machinery.
- Hard Water Stability- SMART CUT KOOL should be stable in all water conditions. Hard water ions react with coolant additives and reduce the effectiveness of the coolant solution.
- Mixability. Concentrate SMART CUT KOOL should mix easily or .bloom. into the water. Any difficulty in mixing will not be tolerated by the customer.
- Foam- All water based coolants can potentially foam. SMART CUT KOOL is formulated with defoamers to prevent foaming under most conditions. The proper selection of coolant concentration will help alleviate potential problems.
- Residue- SMART CUT KOOL will not leave a .hard-to-remove. residue on the surface of the machine or substrates. As the water in the coolant. evaporates organic residue will be left on the machines. This residue should not be sticky and should be easily re-dissolved in water.
- Oxidative Stability- High temperatures and pressures will cause changes in the composition of the coolant, such as fragmentation or polymerization of the additives in the coolant formulation. This can decrease the performance of the coolant and create difficult to remove deposits.
- Emulsion Stability. Concentrate SMART CUT KOOL mixes easily with water and should not separate or create an invert on the surface of the coolant mixture. Customers currently using soluble oils may be experiencing particular difficulties with this problem.
- Tramp Oil Rejection- SMART CUT KOOL should reject the tramp oils and way lubricants, which may contaminate the sump. Other coolants which do not reject tramp oils are prone to attack by bacteria and fungal organisms.