After a silicon ingot has been grown it has to be cut, grind and polished to achieve its final end use form. Silicon can be fabricated using the following process

Band Sawing
Diamond band sawing provides fast cutting rates and lower kerf loss on thicker material pieces. In band sawing the material is placed on the machine table which is movable and often powered by metered hydraulics, air over hydraulics, or stepper motors and ball screws.
The band is tensioned on a set of two or more running wheels, one of which is the driver. The work piece fixturing is similar to that required for table sawing.
In solar wafer manufacturing the main purpose of band saws is to cut the incoming polycrataline or monocrytalline silicon ingots into bricks for desired wafer format.
There is a large variety of band saw machines available on the market. In the past while the solar silicon industry was still in its infancy, most manufacturers simply chose to convert band saw machines designed for metal working to be used with diamond band saw blades. Today, specialized band sawing equipment is available to meet the specific demands of solar silicon industry. Typically most diamond band saw blade thickness range from 0.5mm to 1.5mm. Kef loss varies from .040” to .080” depending on grit size of diamond particles and backing thickness. Specialized band saw machines for cutting solar silicon offer cutting band speeds up to 100 m/s and cutting accuracy for dimension variation perpendicularity and parallelism of + / - 0.2mm, less than 0.4mm and 0.3mm. Vertical travel on the band saw machine usually determines the height of the silicon ingot the can be processed. For example band saw machines with 20” wheels and larger allow sawing of silicon from ½” to 18” high and up to 24” long.
Typically the coarsest diamond grit size available for diamond band saw blades is 35/40 grit, and the finest is 180 grit. For rough cutting/squaring of silicon usually 60/80 grit is recommended. For final slicing/cropping finer grit size such as 100/120 mesh is recommended to produce finer cut and smoother surface finish quality.
High cutting rates can be produced with diamond band sawing in .1 to .2 cubic inches per minute when cutting silicon. The best surface finish that can be obtained with diamond band saw is about 32 RMS and usually requires secondary operations to obtain precise flatness and finish. The fast cutting rates combined with lower kerf loss on thicker material sections is one of the main advantages of diamond band saw process.
Some of the disadvantages include chip out at end of the cut, kerf (sludge) removal and machine war. Sludge of material debris develops after several hours of cutting. This requires use of filtering and settling techniques to remove this cutting waste. The chipping problem may be frequently resolved or minimized by use of waxed body at ed of the cut.

Band Slicing
Kerf rates a s low as .012” can be obtained using diamond band saw slicing blades and techniques. Typically the diamond bands when mounted on sophisticated automatic indexing saws, can produce wafers comparable to ID annular sawing. Tolerances as close as .001” with no secondary finishing required.
Grinding and Polishing
After the silicon blocks have been squared and cropped. The next step involves surface grinding and polishing, before they are ready to be sliced in wire saw. This is a necessary step and operation. Since the squaring and cropping process introduces subsurface damages that may possibly affect the yield in the wafering process. Evidence shows that polished and etched silicon bricks typically exhibit better surface finish quality at wafer edges by as much as 10 to 100. Hence increasing wafer strength by 33 percent. Also the silicon brick grinding and polishing process reduces the time and effort needed to handle the material, as well as reducing the possibility of wafer brakeage in consecutive processing steps. Lastly, processing the material relieves the sharp corners that may evolve during squaring.
Oscillating Wire Slurry & Diamond Wire Saws
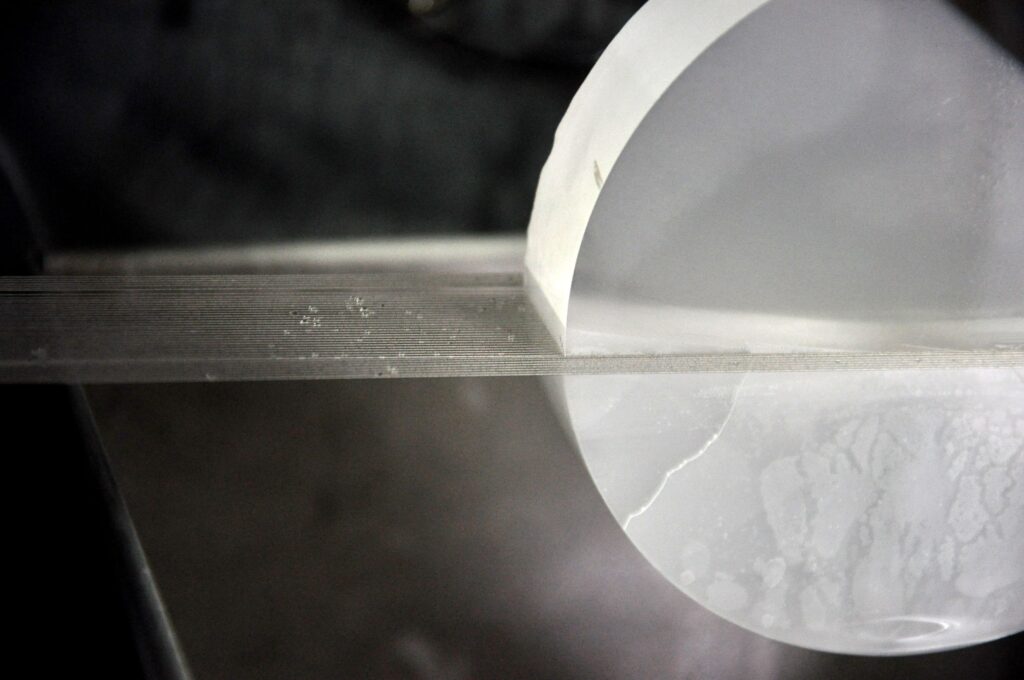
Wire saws provide the most accurate cutting with the least amount of surface damage and chipping of material. Today wire sawing is preferred by majority of solar silicon manufacturers over other technologies/cutting methods. Wire saw operates similarly to horizontal hack saw, where head containing a pack of blades lengths of plain edge stainless or spring steel mounted parallel to head travel oscillates back and forth over the work piece or pieces which are mounted on a bed. The bed can be fed up into the blades at selected pressures. A series of nozzles apply a flow of abrasive slurry (grains of silicon carbide or other abrasive in a liquid vehicle.
That provide a cutting or lapping action between the blades and material. The wire saw allows slicing of hundreds of wafers simultaneously with the same continuous wire. For the most part today abrasives are used and preferred over diamond for cutting silicon. Although use of wire bonded with diamond offers many advantages in terms of faster cutting speed (frequently triple the speed) and improved surface finish quality (less secondary operations such as polishing). Due to the pullouts of diamond crystals/particles, the cutting life is short and costly for high production scenario.
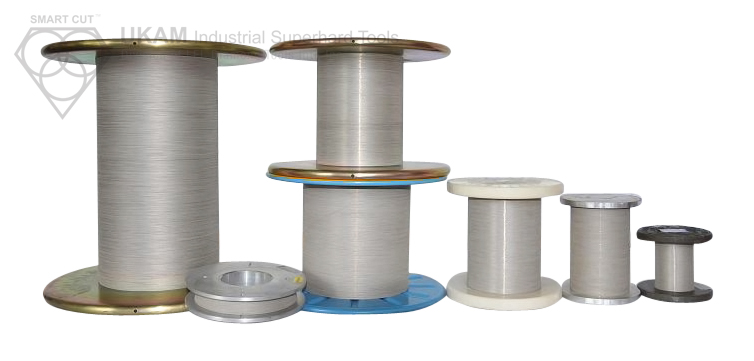
For this reason, most silicon manufacturers utilize copper plated piano wires designed to trap abrasive particles (such as alumina or SiC) suspended in mechanical oil or water based coolant. To provide the cutting action and lubrication of the moving wire. The wire diameter frequently used is smaller than 0.15mm and cutting kerf is about 0.19mm and 0.15mm and smaller. Abrasive slurry grit size varies from 1000 to 250 grit. Viscosity and continous mixing of the slurry must be maintained in order to produces consistent results.
Wire is would around 2, 3,or 4 grooved mandresl in order to allow multiple loops for simultaneous slicing of the same ingot. When the looped wire is running across the ingot, the abrasive particles impeded the soft surface of the piano wire will slowly lap/grind off silicon on micro level (bit by bit). The cutting action is done by reciprocating motion. The wire is used once, and replaced with a new roll.
Typically this type of wire saw can travel at surface speed of 6 mm/sec. The wire moves forward for abut 300mm and this is retraced for abut 200mm. Net advance of the new wire is at an average speed of 2 m/sec with about 100 m new wire passed through each cycle. The wire can run continuously for more than 300 km long. More than 500 slices can be sawn simultaneously. In a production environment 8” (200mm) silicon boul in leas than 8 hours and 12” (300mm) boul in less than 12 hours.
ID sawing
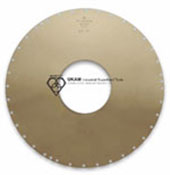
The tension of the blade is provided by the strength to resist deflection duringing sawing with only a fraction of the cross section of peripheral wheels. A single layer of very fine diamond powder in range of 150 to 600 mesh is bonded to the leading edge of the pening and roughly 1/8” down each side by diamond deposition method.
The silicon material workpeice is suspended inside the opening and then accurately fend into the cutting edge. The fixture remains rigid yet gives up wafers freely after they have been sliced. Typically for this application the silicon ingots are mounted on inexpensive disposable carbon bars with a low temperature non loading wax or epoxy.
ID blades limit the size of the silicon work piece by design. The material must be small enough to fit into the opening. , while the distance from the cutting edge to the mounting ring determines the depth of cut. When the diameters of silicon ingots used to be smaller than 8 inches, this cutting method was the industry standard for many years. Allowing high cutting efficiency. The 8” silicon ingot could be typically cut within ten minutes. However, with increased diameter of silicon ingots used today such as 8” to 12”. The industry has for the most part moved away from ID sawing because the thin blade cannot support the distance of cutting. At the same time inside diameter diamond blades can cut only one slice at time, and do not have the cutting efficiency and sped as wire saws.
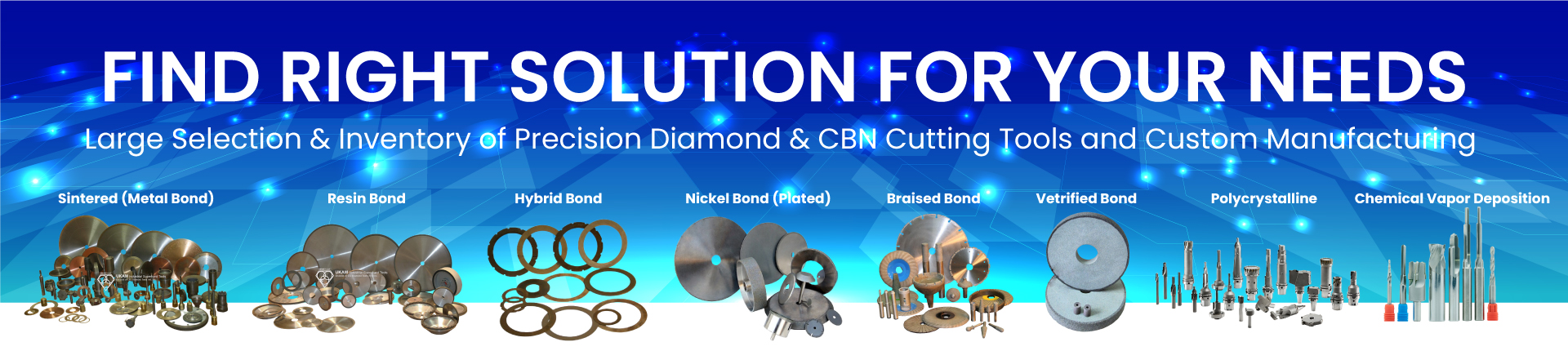