The bond is the agent that keeps the diamond or CBN (cubic boron nitride) crystals in place. Its a matrix that consists of various powders (whether metal, phenolic resin or ceramic). Its job is to release the diamond crystals it hold in a controlled rate to obtain the clients desired objectives. Whether its best surface finish quality, fast cutting speed (certain yield), and long life (economics/return on investment).
The diamond itself does the actual cutting. Bond matrix function is to retain and expose diamond. These two goals can often contradict and even interfere with each other. However, choice of the right bond grading assures that the diamond grit will be held until the maximum cutting value has been obtained. If its too hard, dull diamonds will be held tool long resulting in glazing of the tool which means slow cutting and loss in productivity. For example a hard bond matrix can retain diamond crystals by burying them. If the bond is too soft, the bond matrix will lose diamond crystals by overly exposing them, resulting in premature loss and hence short tool life.
The indication of this premature loss of diamond is deep pocket left behind. The presence of many pockets means the diamond is wasted without being used. Each diamond must protrude high to cut fast with low resistance. In order to cut efficiently not only diamond must be strong enough to withstand the impact, but also it should be adhered in the matrix firmly. Penetration into the material must be deep enough to allow the micro chipping, but shallow enough to prevent diamond shattering.
In order to keep distinct difference between these two goals the diamond is frequently coated or brazed in order to improve its retention so the matrix wear rate can be independently adjusted to allow the diamond to protrude properly
Function of Bond Matrix:
-
provide adequate diamond crystal retention without premature pullouts
-
allow controlled bond erosion, gradually exposing diamond crystals into the work zone
-
provide sufficient strength to ensure optimal transfer of energy from the spindle to the material being worked on
-
provide adequate heat dissipation
bonds can be further classified based on if its single or multiple layered. A single layer bond is a coating with only one layer of diamond crystal attached to steel body. Once that layer of diamond crystal is worn, the tool is finished. Multiple layered bond has usually hundreds of bond layers impregnated in the bond matrix, when one layer of crystal wears, looses its sharp point, disintegrates and falls out. A new layer of fresh diamond crystal protrudes and starts working in the cutting zone, taking its place.
Bond Hardness
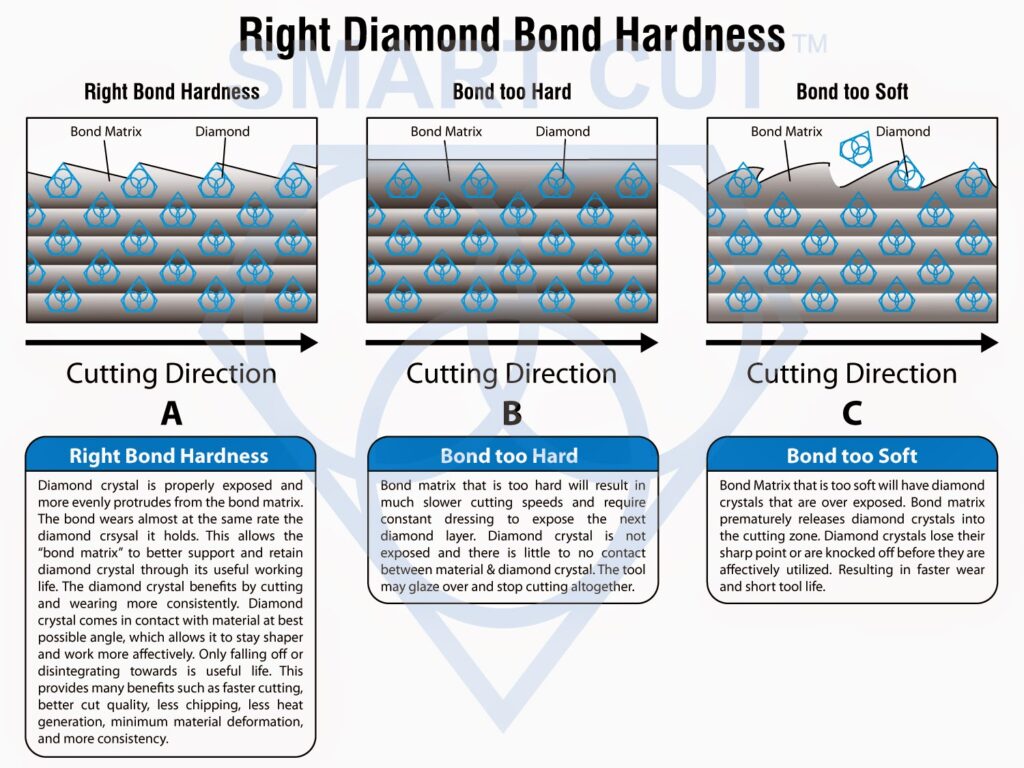
Right Bond Hardness
Diamond crystal is properly exposed and more evenly protrudes from the bond matrix. The bond wears almost at the same rate as the diamond crystal it holds. This allows the "bond matrix" to better support and retain and diamond crystal through its useful working life. the diamond crystal benefits by cutting and wearing more consistently. Diamond crystal comes in contact with material at best possible angle, which allows it to stay sharper and work more affectively. Only falling off or disintegrating towards its useful life. this provides many benefits such as faster cutting, better cut quality, less chipping, less heat generation, minimum material deformation, and more consistency.
Bond too Hard
Bond matrix that is too hard will result in much slower cutting speeds and require constant dressing to expose the next diamond layer. diamond crystal is not exposed and there is little to no contact between material and diamond crystal. The tool may glaze over and stop cutting altogether.
Bond too Soft
Bond matrix that is too soft will have diamond crystals that are over exposed. Bond matrix prematurely releases diamond crystals into the cutting zone. Diamond crystals lose their sharp point or are knocked off. Before they are affectively utilized. Resulting in faster wear and short tool life.
The following Bond Types are available for use in Diamond Tools:
-
Sintered (metal bond)
-
Resin Bond
-
Electroplated (nickel bond)
-
Vitrified Bond
-
Brazed Bond
-
Hybrid Bond
Each bond is made utilizing different technological process, using different base bonding material, addition components or fillers, as well as different type of diamond crystal. For this reason each bond family behaves differently and brings certain strengths to the table as well as weaknesses. Which bond to use would depend on clients objectives, material being processes, equipment used on, and overall environment the tool will be implemented. Its is the job of both the client and the diamond tool maker to work together to determine right bond type and its characteristics for each application. The client must provide as much information as possible to the manufacturer, who will use their experience (working with previous clients) and their analytic approach to determine the optimal tool parameters and usage process for the given application.
Certain tool specification (diamond grit size, concentration, bond hardness, etc) that can produce desired output, can be a disaster when used with another bond type. The two are almost never comparable. For example 120 mesh resin bond diamond cut off wheel can provide
just right cutting speed and surface finish on glass and ceramic tubing. The same mesh/grit size sintered (metal bond) wheel would produce excessive amount of chipping. It would take equivalent of 600 mesh/grit in sintered (metal bond) and higher diamond concentration to achieve somewhat similar cut quality. Even then it would not be possible to achieve same surface finish/chipping level with a metal bond wheel, nor come even close to the cutting speed resin bond can provide. Its like comparing oranges to apples. They are in essence both fruit, but come from two very different families.
Selecting Optimal Bond Type for your Application
Material Type (composition, hardness, brittleness, shape/geometry) will usually most influence the possible bond options. While this is not the only important variable in the overall equation. This will definitely weed out the bond options that would not be compatible.
Equipment/Machinery to be Used - machinery functionality, RPM's range and capability to adjust pressure/feed will even further narrow down the choice. Each bond family requires different rpm ranges in order to provide optimum level of performance. Resin bond must be used at fast speeds in order to wear and expose their diamond crystals, that is usually much higher then their sintered (metal bond) counterparts. If the RPM's of the machine intended to be used with this tool does not have the necessary speed range, then the performance of the tool will be marginal at best. Diamond crystals will glaze over and lose their sharp points fast, the tool would have to be constantly dressed in order to just get by. By the same token a sintered (metal bond) tool when used at speeds faster then recommended, will become much harder. The diamond crystals will not be able to affectively perform, glazing over metal bond matrix will be smeared over them, causing excessive heat.
Clients Objective (desired end result) - Clients desired end result is the next step in the bond type & tool selection process. Clients come from many different industries and organization types and sizes. The desired output/yield objectives will vary depending if the application is prototyping/R & D or high volume production operation. Furthermore different clients require different tolerance ranges, surface finish quality, chipping level, tool life, tool cost, and level of consistency. Its not uncommon for different clients to select different tool specification and bond for same application. While the material type and equipment used may have limited the range of choices available.
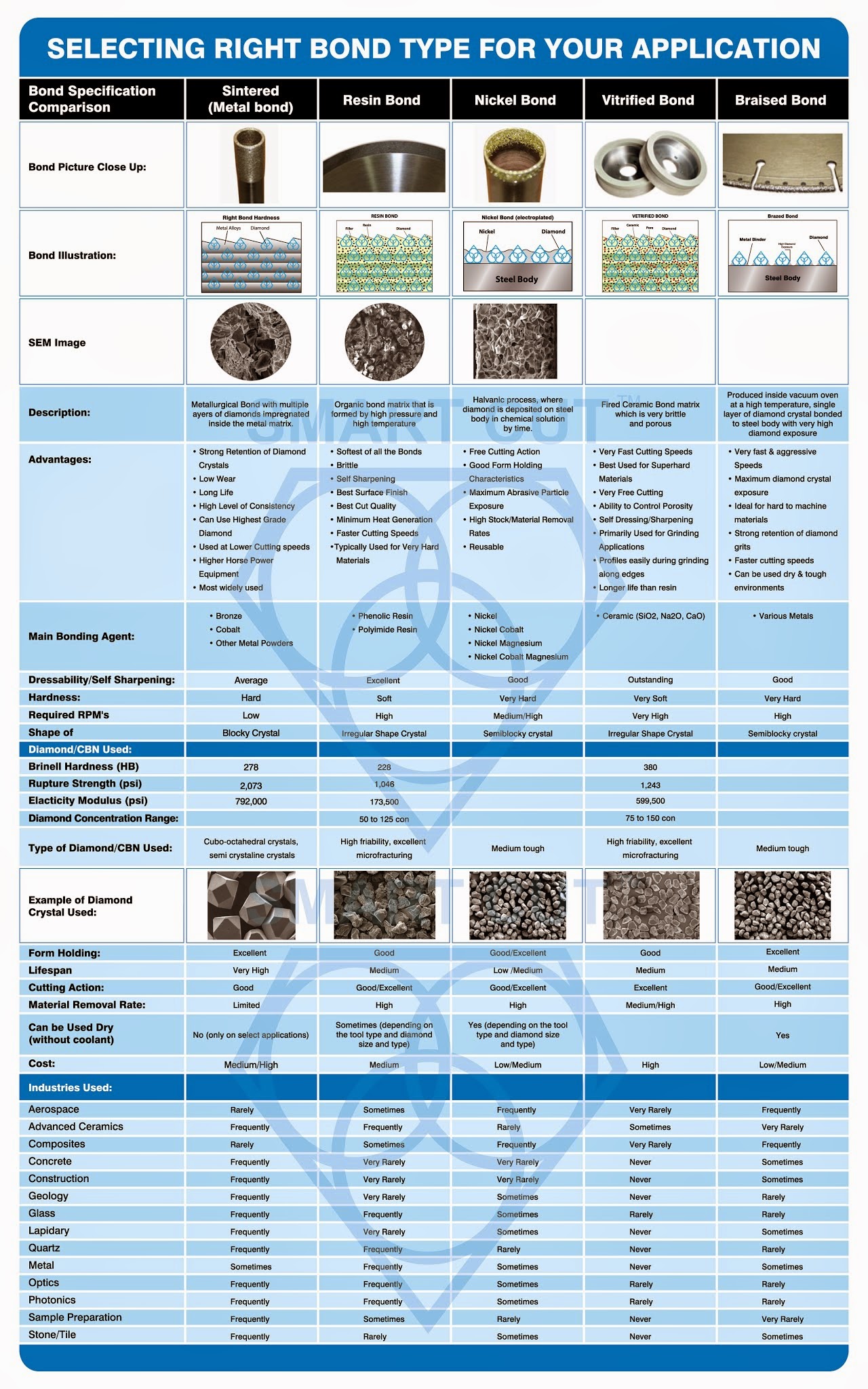
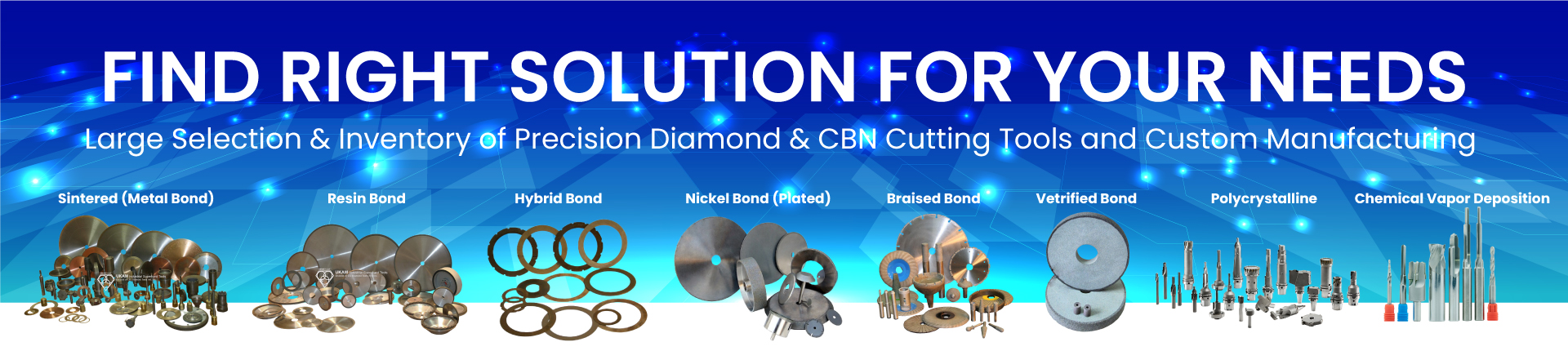