Coolant supply position and pressure is critical to minimize chipping, and maintain consistent and acceptable cut quality.
Coolant serves many functions in precision cutting operation:
-
Cools blade diamond section and material being cut
-
Provides lubrication to minimize friction between blade and material
-
Washes out and removes powder residue and swarf from cutting process

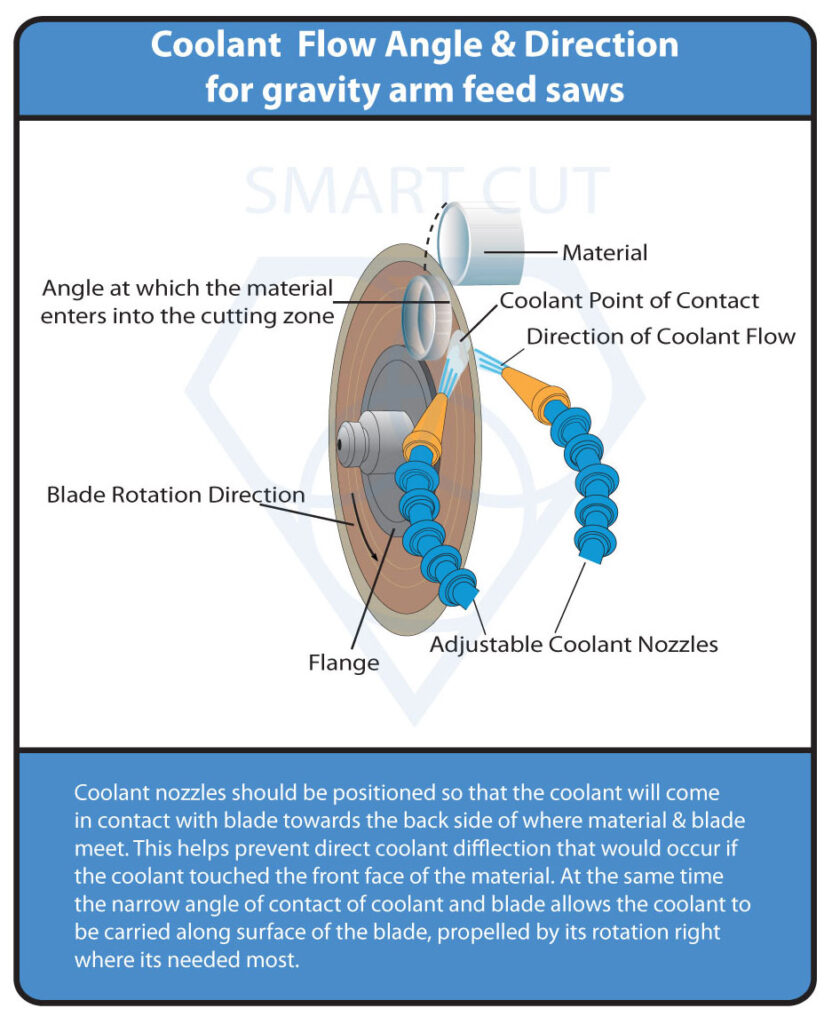

hard, dense & brittle materials the coolant flow direction and position will play a major role in determining blade life and performance. Dual nozzle configuration is best suited to supply adequate amount of coolant at point of contact between blade and material. Coolant should be pointed at blade point of contact and leading edge of blade. The dual nozzle system provides two separate streams of coolant into cutting zone at angle of cutting edge of the blade. Each stream will cool one side of the blade. The nozzles should be as close as possible to the point where the blade enters the material/sample. Coolant flow should blast with high velocity into the kerf to improve removing debris.
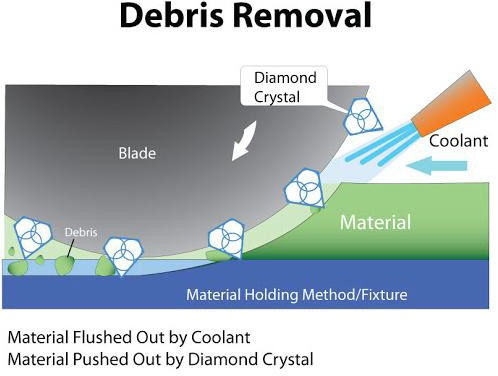
Wide kerfs an premature blade water is a result of improper coolant amount or flow applied at cutting zone. By correctly position the coolant stream in front of the blade, the coolant will flow on top of the material. In addition, coolant will be drawn into the kef
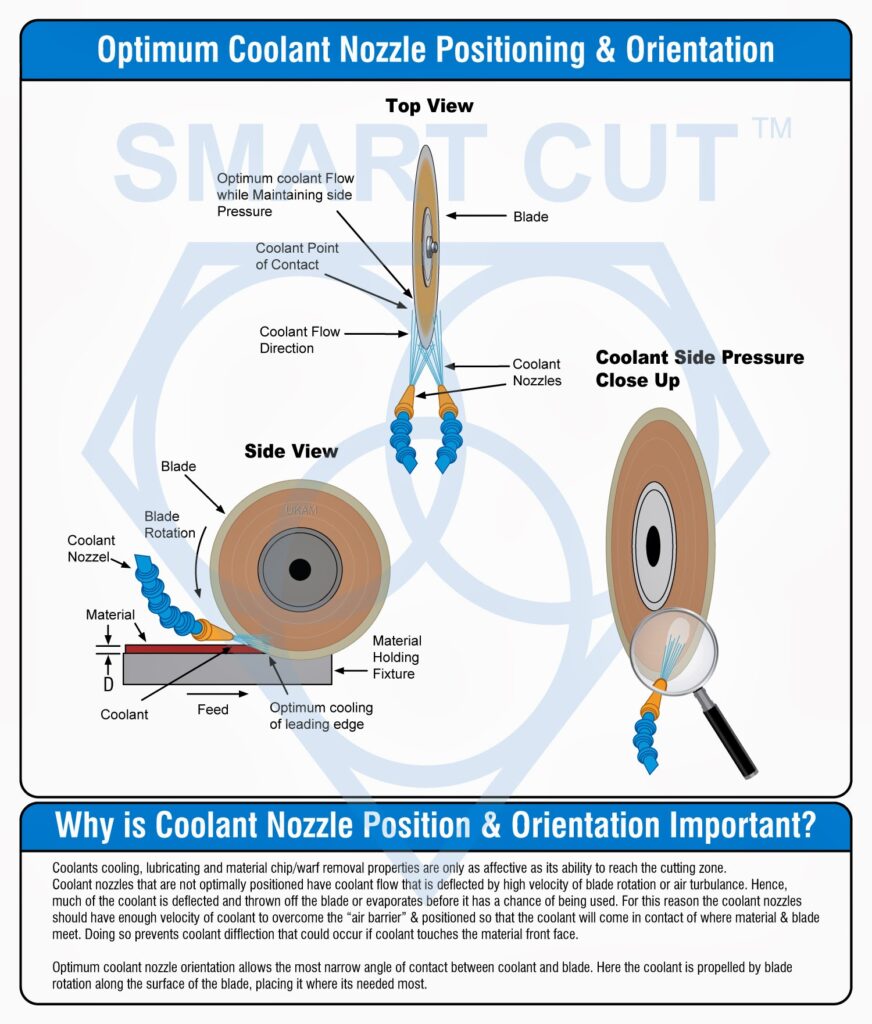
The blade should enter into the material “cutting down”. As the blade penetrates the surface of the material, chips removed by diamond particles become smaller the deeper the blade penetrates. This cutting direction is most optimal to provide best cut quality. When cutting in the opposite direction the blade enters the substrate almost tangential. The chips removed are being small and start but their size increases to maximize where the blade exits the face of the material/sample. Much chipping at the surface is the result. Cutting in the up direction creates more edge chipping than cutting down. The spindle torque is noticed to be the large cutting up than when cutting down.
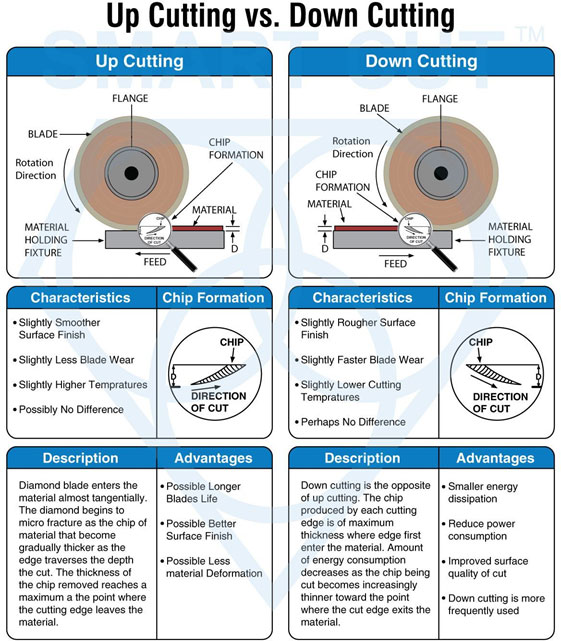
Doing so would lower the surface tension of the water and help coolant better penetrate the full depth of kef. Furthermore the coolant would act as a lubricant and aid in minimizing the load created by cutting process. Another solution would involve use of specialized flange set.
RECIRCULATING COOLANT SYSTEMS
Recalculating coolant systems, require filtering to remove the swarf particles created during cutting process. These coolants systems typically use either cartridge, centrifugal, or cascade. Which process to use will depend on your application. Excessive amount of swarf particles mixed in coolant will slow heat transfer of coolant and may cause surface damage to material being cut. Coolant system must be constantly controlled and monitored in order to insure process consistency
Coolant Temperature
Coolant temperature will also have an effect on blade life and cut quality. Typically coolant temperatures of 50 degrees F (10 degrees Celsius) will provide best results. White coolant temperatures above 80 degrees F (27 C) should be avoided. Refrigeration of the coolant system can be used with most coolant systems and will provide best results.
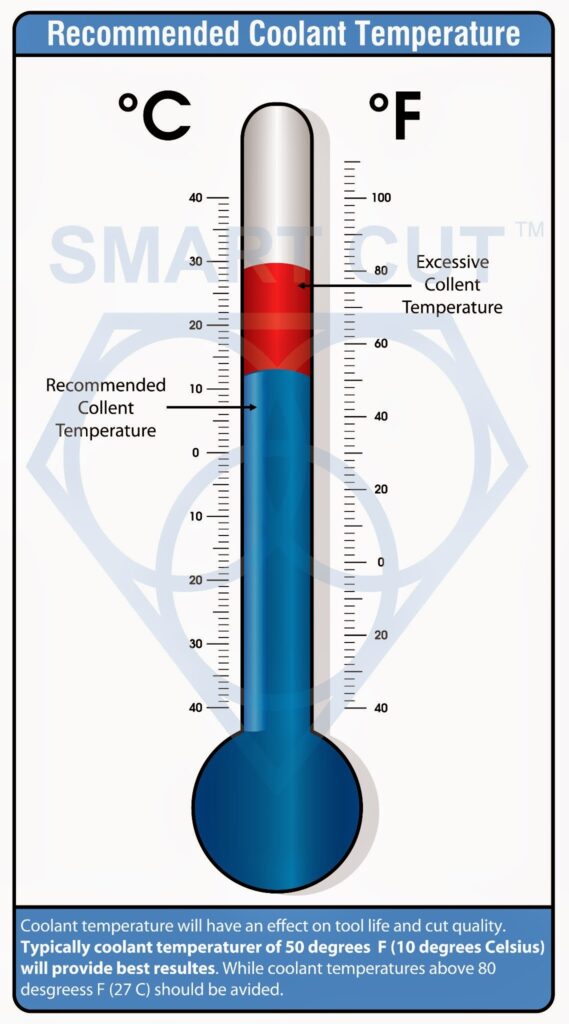
COOLANT MAINTENANCE & OPTIMIZATION
Coolant is one of the most overlooked variables in the overall precision process. Effective and proper use of coolant and recalculating coolant system will pay off in terms of improved surface finish quality, increased blade life and more consistent cutting results. Coolant does more than just cool the blade and material, its other more important roles include: lubrication, flush away swarf particles.
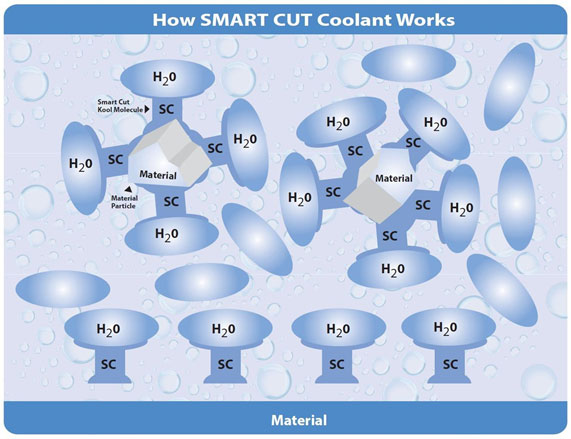
For most effective use of coolant the quality of water being used, coolant concentration, and maintenance of the coolant tank makes a difference. Different geographic areas have different water harnesses. Water containing less than six grains of dissolved minerals per gallon is considered soft water, water containing more than seventeen grains per gallon is considered hard. The best coolant water to use in a coolant system is chemically pure water, which is free of all dissolved solids. Chemically pure water and reverse osmosis. Reverse osmosis is the method most recommended by coolant manufacturers, however not always available. De-ionized water offers much improvement over available plant water.
Water in the tank can evaporate and remaining water can become harder. Hard water affects coolant capabilities in many ways decreased capability to the rust inhibitor, increased foaming, formation of a sticky residue, and increased bacteria counts. Coolant concentration should be controlled and maintained to ensure that the coolant is being used at optimum efficiency. Too little coolant in the tank will lead to corrosion and rancidity, while too high of a concentration can also cause foaming. Maintenance of the re-circulating tank is also critical to coolant performance. Cleaning he tank is a dirty job, but if done often enough and thoroughly, it can increase the performance of your dicing saw. Keeping he coolant tank clean will ensure that you are getting the most form your coolant, keeping corrosion and bacterial growth a bay while providing the necessary coolant, lubrication and protection of your blades and material.

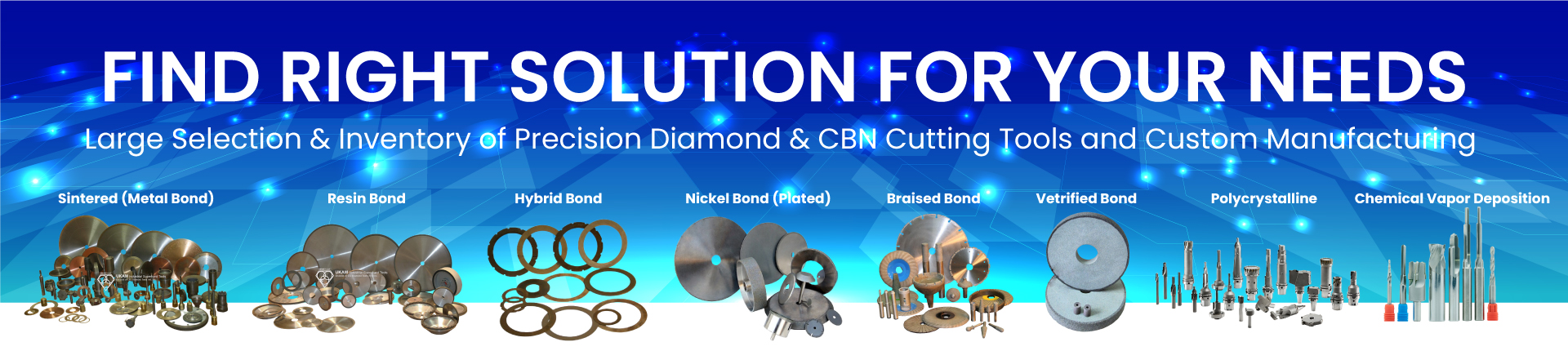