Common Materials - FR4 and epoxy mold compound.
Common Materials - Copper, HTCC (High Temperature Co-fired Ceramics), LTCC (Low Temperature Co-fired Ceramics).
DICING SOLUTIONS FOR PACKAGE SINGULATION
BGA (Ball-Grid Array)
Typical Concerns:
-
Cut quality
-
chipping
-
burrs
-
slivers
-
protrusions
-
race shorts
-
Blade life
Dicing Blade Recommendation:
-
SMART CUT HYBRID BOND or sintered (metal bond) series
-
Diamond size: 30 - 55 microns
-
Blade Thickness: .008” - .014”
Dicing Process Recommendations:
-
Feed rate: 50-250 mm/sec
-
Spindle speed: 20-40 krpm depending on blade O.D.
-
Multi panel mounting on UV tape
-
Minimal dressing so as not to create a large radius on the blade edge
QFN (Quad Flat No Lead)
Common Materials - C194 and epoxy mold compound.
Typical Concerns:
-
Chipping
-
Burrs
-
Lead smearing
-
Melting
Dicing Blade Recommendation:
-
SMART CUT HYBRID BOND or sintered (metal bond) series
-
Diamond grit size: 45 - 88 microns
-
Thickness: .008” - .020”
Dicing Process Recommendations:
-
Feed rate: Half Etched substrates 30-75 mm/sec, Full Copper substrates 15-30 mm/sec
-
Spindle speed: 22-35 krpm depending on blade O.D.
-
Multi panel mounting on UV tape
-
Override process over one substrate to reach final feed rate
LED (Light-Emitting Diode)
Common Materials - Copper, HTCC (High Temperature Co-fired Ceramics), LTCC (Low Temperature Co-fired Ceramics).
Typical Concerns:
-
Copper burrs
-
End of blade life due to limited exposure
-
Throughput (maximize UPH)
Dicing Blade Recommendation:
-
SMART CUT HYBRID BOND or Nickel Bond series
-
Diamond size: 10,13 & 17 microns
-
Thickness: .003” - .008”
Dicing Process Recommendations:
-
Feed rate: 80-150 mm/sec
-
Spindle speed: 25-30 krpm
-
Multi panel mounting on UV tape
CMOS (Complementary Metal-Oxide Semiconductor)
Common Materials - Borosilicate Glass, HTCC (High Temperature Co-fired Ceramics).
DWDM (Dense Wavelength Division Mulitplexing) Filters
Common materials: Glass, Quartz.
Typical Concerns:
-
Top-side and back-side chipping
-
Cut perpendicularity
-
Kerf side surface finish
Dicing Blade Recommendation:
-
SMART CUT series Resin, HYBRID, & Sintered (metal bond) blades
-
Diamond size: 30 - 45 microns (resin) and 7 - 15 microns (sintered)
-
Thickness: .006" - .012”
Dicing Process Recommendations:
-
Feed rate: 4 - 20 mm/sec
-
Spindle speed: 20 - 30 krpm (2") 10 - 15 krpm (4")
-
Dicing synthetic water soluble coolants may reduce chipping and improve surface finish
HDD (Hard Disk Drive)
Common Material: AlTic (Aluminum Titanium Carbon), Ferrite Ceramic.
Typical Concerns:
-
High Mechanical (internal) stress
-
burrs
-
large kerf width
-
lack of accuracy
Dicing Process Recommendations:
The MR head substrate is made of ferromagnetic ceramic material, which has an extremely hard wear resistance and excellent magnetic properties. a typical MR substrate is AlTiC. Substrate thickness typically ranges from 200 to 300 microns. Substrates for HDD read heads require machining after being sintered into bars or sheets. Than they have to be diced into very small unit with very high precision tolerances.
Semiconductor Wafer
Common Material: Silicon, LiNbO3 (Lithium Niobate).
Typical Concerns:
-
Top-side and back-side chipping
-
Cracking
-
Wafer contamination due to ESD issues and poor cleaning
Dicing Blade Recommendation:
-
SMART CUT Nickel Bond or HYBRID series
-
Diamond size: 4 - 6 microns
-
Thickness: .0008” - .0016”
Dicing Process Recommendations:
-
Feed rate: 25 - 75 mm/sec
-
Spindle speed: 30 - 50 krpm
-
Mounting: Blue or UV tape
-
Cooling type: DI water with and without additives
-
Carbon dioxide bubbler is optional
Silicon & GaAs are the two most common materials used for semiconductor wafers. Wafers are typically available in sizes up to 12" in diameter, with 6" and 8" most popular. Typical thicknesses are between 100 - 650 microns.
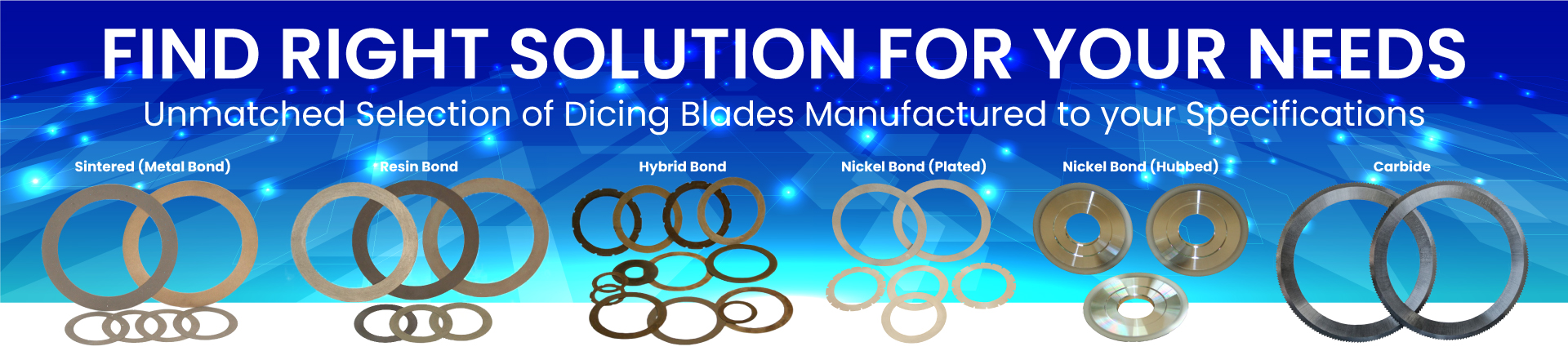
ARE YOU USING RIGHT TOOLS
FOR YOUR APPLICATION?
HAVING ISSUES WITH
YOUR CURRENT TOOLS?
02
Jun
How to Selecting Right Diamond Tools for your application
Share this Article with Friend or Colleague
One of the most critical factors in successful diamond too...
02
Jun
How to properly use Diamond Tools
Share this Article with Friend or Colleague
UKAM Industrial Superhard Tools manufactures precision dia...
02
Jun
Why use diamond
Share this Article with Friend or Colleague
Diamond is the hardest material known to man kind. When...
02
Jun
How Diamond Tools Work
Share this Article with Friend or Colleague
Diamond will work all types of materials from hardness of ...
02
Jun
What is SMART CUT Technology
Share this Article with Friend or Colleague
The sharpest and finest quality diamonds or CBN crystals t...
02
Jun
Diamond Wire Advantages & Application
Share this Article with Friend or Colleague
Diamond Wire saws provide the most accurate cutting with t...
02
Jun
What is Diamond Mesh Size and how to select best one for your application
Share this Article with Friend or Colleague
Diamond grit size can be defined as the size of the diamon...
02
Jun
What is Diamond Concentration and which to use for your application
Share this Article with Friend or Colleague
Life of the diamond tool is primarily controlled by amo...
02
Jun
Diamond crystal quality – you get way you pay for
Share this Article with Friend or Colleague
The size of the diamond crystals, as well as the concentra...
02
Jun
Diamond impact strength
Diamond crystal wear mechanism is dependent on diamond strength. In order to optimize the cutting performance in ...
02
Jun
Diamond Tool Bond Hardness & wear resistance
Share this Article with Friend or Colleague
The main job of the bond matrix is to hold the diamond ...
02
Jun
Material Holding Methods
Material mounting, properly securing material in place is one of the first and most important steps in the micro ...
02
Jun
Material Guide
Share this Article with Friend or Colleague
Learn everything you wanted to know about different mat...
02
Jun
Silicon Fabrication Guide
Share this Article with Friend or Colleague
After a silicon ingot has been grown it has to be cut, ...
02
Jun
Diamond Tool Coolants Why, How, When & Where to Use
Coolant supply position and pressure is critical to minimize chipping, and maintain consistent and acceptable cut quality.
Co...
02
Jun
Diamond vs CBN (cubic boron nitride) Tools
Share this Article with Friend or Colleague
Cubic Boron Nitride (CBN) is a synthetic material that is ...
02
Jun
Dressing Diamond Tools Why, How, When & Where
Share this Article with Friend or Colleague
Dressing is the process of sharpening & exposing diamo...
18
Jul
Get to Know the Diamond Tool Bond Types and Which to use for your application
Share this Article with Friend or Colleague
The bond is the agent that keeps the diamond or CBN (cubic boron nitride) cryst...
04
Aug
RPM’s & Feed Rates
/*! elementor - v3.13.3 - 28-05-2023 */
.elementor-heading-title{padding:0;margin:0;line-height:1}.elementor-widget-heading .elementor-...
04
Aug
What is Surface Finish
Surface finish is typically measured in terms of roughness or smoothness. It influences the appearance, functiona...
04
Aug
What are Tolerances, Accuracy, and repeatability
Tolerances, accuracy, and repeatability are essential concepts in the fields of engineering, manufacturing, and m...
04
Aug
Diamond Tools compared with Abrasive Tools
Diamond tools and abrasive tools are both commonly used in various industries for cutting, grinding, and polishin...
04
Aug
Diamond vs. Laser and Water Jet
Machining with diamond tools and using diamond, laser, and water jet as cutting methods are all different process...
04
Aug
Diamond Wire vs band saw blades and circular blades
Diamond wire, band saw blades, and circular blades are all cutting tools used in various industries for different...
04
Aug
What is Chemical Vapor Deposition and its application
CVD diamond coating takes place in a vacuum chamber using a hot-filament, chemical vapor deposition (CVD) process...
04
Aug
What is Polycrystalline Diamond and its application
PCD tools are used for processing aluminum and aluminum, aluminum alloys, copper, copper alloy, babbitt metal, wo...
04
Aug
What are diamond dressers and their application
Diamond Dressers are used for truing and dressing conventional abrasive and super abrasive (diamond/cbn) wheels. ...
04
Aug
How Diamond Tools are Manufactured
Manufacturing diamond tools involves a series of technological processes to impregnated manmade or natural diamon...
04
Aug
What is the difference between Lapping, Grinding, & Polishing
/*! elementor - v3.15.0 - 09-08-2023 */
.elementor-heading-title{padding:0;margin:0;line-height:1}.elementor-widget-heading .elementor-...